湛江專業(yè)數(shù)控轉臺廠家
發(fā)布時間:2022-09-15 00:33:36
湛江專業(yè)數(shù)控轉臺廠家
由于數(shù)控轉臺中的角接觸球軸承可以同時承受徑向載荷和軸向載荷。應當知道,接觸角是角接觸球軸承中非常重要的參數(shù)。它直接確定角接觸球軸承在軸向上的承載能力。第四軸,數(shù)控轉臺或分度頭完成相等,不相等或連續(xù)的旋轉加工,以完成復雜的表面加工,從而擴大了機床的原始加工范圍。此外,數(shù)控轉臺裝卸裝置,包括可調高度的工具臺面,配有固定導軌和活動導軌。可移動的導軌可以插入到數(shù)控機床工作臺的T型槽中,滑道安裝在滑道上。機床的滑臺和工作臺齊平或稍低,滑臺配有鎖緊螺釘和頂進螺釘,并通過保護蓋將數(shù)控轉臺移入和移出數(shù)控機床,具有良好的安全性,操作方便,效率高。數(shù)控轉臺已經(jīng)形成了社會支持體系,這是市場經(jīng)濟發(fā)展的必然結果,也是提高產(chǎn)品水平,縮短交貨時間,降低成本,大批量生產(chǎn)的途徑。專業(yè)生產(chǎn)和社會合作應成為我國數(shù)控系統(tǒng)配件發(fā)展的方向。
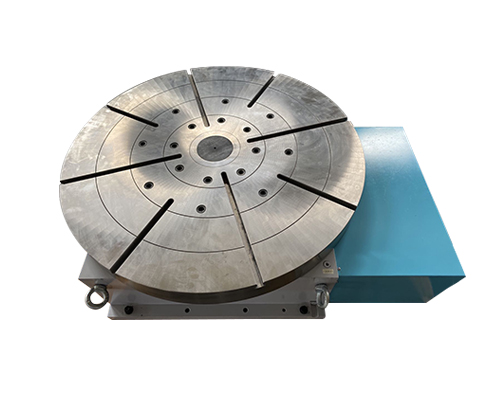
湛江專業(yè)數(shù)控轉臺廠家
數(shù)控轉臺由伺服電機驅動,經(jīng)過齒輪減速后帶動渦輪蝸桿副讓工作臺開始轉動。為消除反向間隙與傳動間隙,通過調整偏心環(huán)消除齒輪嚙合側邊縫隙。一邊的齒輪與蝸桿依靠楔形拉緊圓柱銷進行連接,此種連接方式可以消除軸與套的配合間隙。此種蝸桿的兩邊具備不同的螺距,所以蝸桿齒厚從頭至尾都是逐漸加厚。但是因為相同一邊的螺距是相等的,因此數(shù)控轉臺依然可以保持正常嚙合。而蝸桿偏心軸套調整中心距,從而達到消除蝸桿副間隙目的。當數(shù)控轉臺靜止時,數(shù)控轉臺會處于鎖緊狀態(tài)。目前鎖緊方式有2種:鼠牙盤鎖緊,此種方式只適用于中型或小型數(shù)控轉臺,鼠牙盤鎖緊方式的鎖緊力小。

湛江專業(yè)數(shù)控轉臺廠家
近年來,數(shù)控轉臺的應用受到了很多的重視,在使用之前對產(chǎn)品的配置進行了解才能達到好的使用效果,那么數(shù)控轉臺的配置與使用建議有什么呢,一起來了解一下吧。高硬度的斜齒輪能保證工具的使用時間長。噴水咀可濕潤切割工作面,不使塵粒外揚,使身體免受灰塵帶來的刺激。三檔速度調節(jié)裝置。合理的握把設計,提高工作的舒服度。工具工作時先配上粘盤,然后根據(jù)不同要求配上不同數(shù)目的軟磨片,達到磨光、拋光效果。每天使用前后請注入一定的氣動潤滑油。注油后請使自由運轉幾秒鐘。若能起動便成扭力不足,一定要注意從后進氣口注入氣動油再按氣動工具空轉幾秒便可,扭力可恢復正常。以上就是數(shù)控轉臺的產(chǎn)品配置與使用建議,希望能夠給大家?guī)韼椭肓私飧嘀R歡迎來電咨詢。

湛江專業(yè)數(shù)控轉臺廠家
數(shù)控轉臺工作效率也是比較高的,大家知道電子產(chǎn)品是很重視其散熱的問題,所以數(shù)控轉臺也是要注意其散熱方面的問題。那為什么會出現(xiàn)散熱器過熱的現(xiàn)象呢?下面大家一起來學習數(shù)控轉臺會需要散熱的原因吧。在使用數(shù)控轉臺的時候可能超負荷運轉,使得電流變大,額定功率大于實際功率,致使數(shù)控轉臺的部件過熱。可能是數(shù)控轉臺的設置或者是起步裝置有問題,在啟動的時候能耗轉化率比較低。因為由于數(shù)控轉臺設置的過快或者是起步的裝置有問題,就會容易出現(xiàn)數(shù)控轉臺功率過大,在能耗轉化低的情況下產(chǎn)生熱量。功率設置過高,也會導致數(shù)控轉臺實際需要的功率沒有這么的大,致使超過的功率流失轉化為電能。
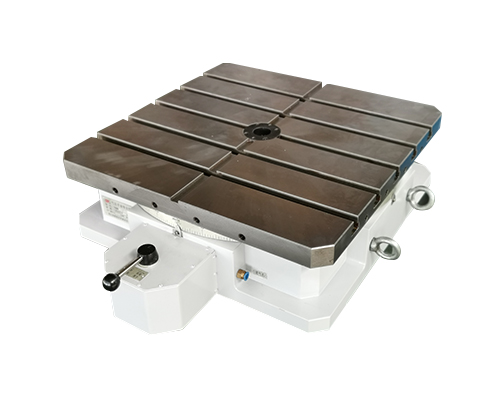
湛江專業(yè)數(shù)控轉臺廠家
數(shù)控轉臺利用靜壓導軌油膜的方法,其實大多數(shù)其實都是無法做到可以非常的滿足精度這樣的要求的,所以就目前來說的話,其實一般采用的方法其實還是刮研這樣的加工方法來進行保證,下面給大家講一下數(shù)控轉臺的刮研方法:刮研方法是數(shù)控轉臺經(jīng)常采用的方法,數(shù)控轉臺一般都會采用運轉平穩(wěn)的靜壓導軌來進行刮研。大型數(shù)控轉臺的靜壓導軌上的油膜厚度其實主要的目的是為了增加其剛性,但是大型數(shù)控轉臺靜壓導軌上的油膜厚度一般只有0.03~0.06毫米之間的范圍數(shù)值,還是屬于比較偏薄的,所以這也就在一定程度上間接的表明了對導軌面的加工精度的要求其實還是屬于比較高的。一般來說的話,其實大型數(shù)控轉臺的底座長度大都是維持在2m以上的長度范圍內,但是因為大型數(shù)控轉臺的底座剛性基本上還是屬于較差的,所以在正式開始進行刮研前,要對導軌進行一個平面度的測量以及調整,這步工作的實施有利于減少后面要進行刮研的工作量。